„Wir werden ganz neue Produkte schaffen“
Schneller, günstiger, nachhaltiger: Warum die Kriwat GmbH auf die digitale Einlagenproduktion mit SLS-3D-Druck setzt.
Die Orthopädiebranche sieht einem ernsthaften Arbeitskräftemangel entgegen. Um die Kriwat GmbH zukunftssicher aufzustellen, hat die Kieler Firma einen digitalen Arbeitsprozess zur Produktion von Einlagen mit SLS-3D-Druck (selektives Lasersintern) entwickelt.
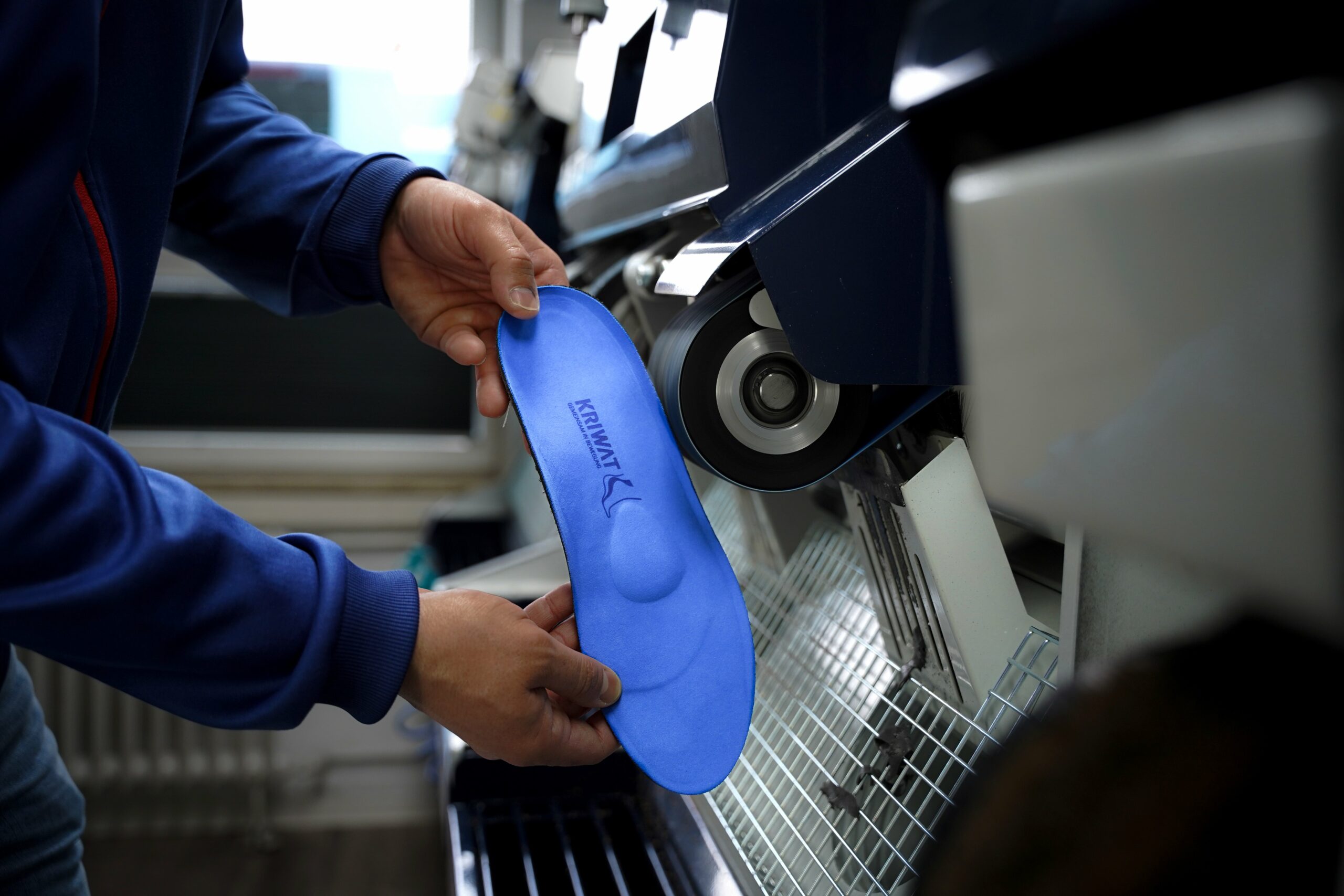
Feinschliff der 3D-gedruckten Einlage
Der traditionelle Prozess der Einlagenfertigung ist bekannt: Mit Hilfe einer Schaumform wird der Abdruck des Fußes genommen. Die Form wird dann mit flüssigen Chemikalien gefüllt, um die Fußform nachzubilden „Das hat mich während meiner Ausbildung sehr gestört. Vieles musste mit Chemie hergestellt werden“, erklärt Lais Kriwat, Orthopädieschuhtechnikmeister und Geschäftsführer des Kieler Einlagenspezialisten. „Viele Sachen mussten an der Schleifmaschine bearbeitet werden. Da hat man immer sehr, sehr viel Kontakt mit Chemikalien und vielen Stäuben. Deswegen habe ich mir als Ziel gesetzt, dass ich einen anderen Weg einschlagen will, um den Kontakt mit Chemikalien zu reduzieren.“
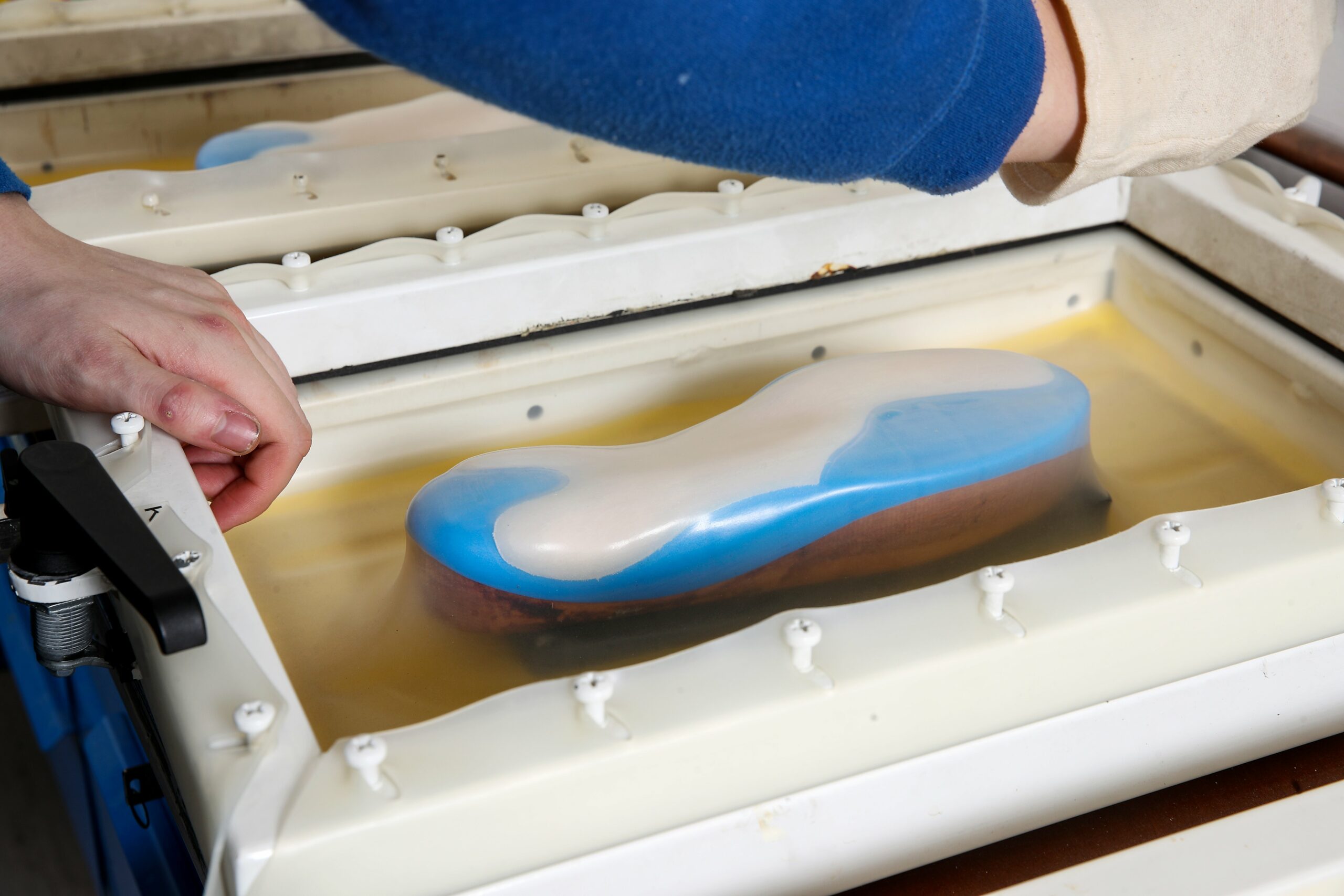
Traditionelle Herstellung einer Einlage
Als Neueinsteiger in der Branche erlebte Kriwat die Herausforderungen des traditionellen Arbeitsprozesses aus erster Hand. Er erkannte, dass Veränderungen notwendig waren, um auf dem Arbeitsmarkt relevant zu bleiben. „Es ist schwer, Personen zu finden, die unser Handwerk noch ausüben wollen, und diese zu interessieren, dieses Handwerk am Ende als Job zu machen. Deswegen wollen wir den Job interessant gestalten. Und da sind neue Technologien enorm wichtig.“
Die 3D-Druck-Anfänge
Lais Kriwat begann 2017 mit 3D-Druck zu experimentieren, als er auf einem kleinen Schmelzschichtungs-3D-Drucker (FDM) Hobbyprojekte und Prototypen druckte. Nachdem er sich mit 3D-Design und -Druck vertraut gemacht hatte, suchte er nach Wegen, diese in das Familiengeschäft zu integrieren. Ein Drucker für Modelle in Lebensgröße eröffnete völlig neue Möglichkeiten für die Orthesenfertigung. Kriwat erschloss Schritt für Schritt neue Anwendungen, bevor er sich schließlich dem Kerngeschäft des Unternehmens zuwandte, der Herstellung von Einlagen.

Schritt für Schritt digitalisierte er den Arbeitsprozess der Einlagenproduktion und validierte die Endprodukte durch interne und Kundentests. Im neuen digitalen Arbeitsablauf werden manuelle Fußabdrucke durch
3D-Scans ersetzt und die lange Liste manueller Arbeitsschritte wird dank digitalem Design und 3D-Druck verkürzt. Die 3D-gedruckten Teile werden mit dem traditionellen Prozess kombiniert, um das Endprodukt zu fertigen.
Vorteile bei der Einlagenproduktion
Mit zwei SLS-3D-Druckern des Typs Fuse 1+ 30W von der Firma Formlabs und Nylon 11 Powder stellte Kriwat individuelle Einlagenkerne und komplette Einlagen her. Vor dem Umstieg auf die digitale Produktion war es für den Fachmann der Nachweis entscheidend, dass der neue Arbeitsprozess sowohl für das Unternehmen als auch seine Kundschaft beträchtliche Vorteile mitbringt.
Der neue Arbeitsablauf macht es möglich, aus einem 3D-Scan, mit dem sich die Form eines Fußes genauer und vollständiger abbilden lässt als bei einem Abdruck, noch am selben Tag ein digitales Modell zu kreieren und dieses in einem Druckauftrag zusammen mit weiteren Einlagen über Nacht zu drucken. Danach kann Kriwats Team die Teile nachbearbeiten, mittels des traditionellen Arbeitsablaufs die Einlage um den Kern herum fertigen und die gesamte Einlage am nächsten Tag fertigstellen.
„Jetzt haben wir die Möglichkeit, innerhalb von 24 Stunden eine perfekt passende Einlage für den Patienten zu schaffen. Das ist etwas, was für uns natürlich einen extremen Vorteil bietet. Denn am Ende ist das Wichtigste der Patient, der ein Problem hat und den wir innerhalb von kürzester Zeit perfekt versorgen können.“
Kosteneinsparungen
Verglichen mit traditionellem Handwerk bietet der neue digitale Arbeitsablauf finanzielle Vorteile. Viele digitale Arbeitsschritte erfordern weder Material noch langwierige Handarbeiten. Bei Kriwats Produktionsvolumen rechnet sich der einmalige Erwerb eines 3D-Scanners und der Designsoftware im Vergleich zu den großen Ausgaben für Trittschaum und flüssige Chemikalien.
Außerdem können die Mitarbeitenden dank des schnelleren Arbeitsprozesses mehr Fälle pro Tag bearbeiten. Lais Kriwat schätzt, dass sich die Produktionskosten dank des 3D-Drucks um etwa 15 bis 17 % reduzierten.
Das Sparpotenzial lag frühzeitig auf der Hand. Gleichwohl lagen die meisten SLS-Drucklösungen mit Preisen im sechsstelligen Bereich außerhalb des Budgets. Der SLS-Drucker Fuse 1+ 30W sei das einzige Gerät gewesen, das zu einem erschwinglichen Preis die gesuchte industrielle Leistung bot.

Alltagseinlage
Vereinfachter Arbeitsablauf
Der SLS-3D-Druck bietet viele Funktionen zur Vereinfachung der Einlagenfertigung. Dank des selbststützenden Druckverfahrens können zahlreiche Einlagen in einem Auftrag gedruckt werden, was den Prozess optimiert und Kosten senkt. Die Nylonteile haben eine leicht raue Oberflächenbeschaffenheit. Dadurch eignen sie sich für das Bekleben mit Zusatzstoffen und Deckschichten für die verschiedenartigen Endprodukte. Außerdem können sie zerspant und geschliffen werden, um die gewünschte Oberflächenqualität für das Endprodukt zu erzielen. Die 3D-gedruckten Einlagen und Einlagenkerne werden mit Deckschichten und anderen Materialien kombiniert, um das Endprodukt zu fertigen.
Verbesserte Logistik
Die Digitalisierung vereinfacht auch das Logistikmanagement. In ihrer Hamburger Filiale hat die Kriwat GmbH mittlerweile 3D-Scanner, dank derer die Daten digital an den Hauptsitz in Kiel versendet werden können, wo die Endprodukte entworfen werden. In der Vergangenheit mussten die physischen Abdrücke zeitraubend und kostspielig nach Kiel transportiert werden.
Nachhaltigkeit
Durch den digitalen Arbeitsablauf wird für die Fertigung des Endprodukts weitaus weniger Material benötigt. Kriwat muss nicht mehr Tausende von Fußmodellen, Reste unbenutzten Trittschaumes und Chemieabfälle entsorgen. Ungesintertes Pulver kann für den nächsten Auftrag recycelt werden, so dass ein Kreislaufprozess entsteht, durch den sich Abfälle reduzieren oder sogar gänzlich vermeiden lassen.
„Nachhaltigkeit ist für meine Generation das wichtigste Thema. Mein Ziel war, dass wir am Ende nicht so viel Material entsorgen müssen. Wir haben hier eine Plastiktonne, wo ich mir zum Ziel gesetzt hatte, dass sie nicht mehr wöchentlich geleert werden müsste, sondern wir den Abfall so minimieren, dass man sie nur noch alle vier Wochen leeren muss. Ich wollte auch den Einsatz von Chemikalien reduzieren und weniger davon entsorgen. Die SLS-Technologie ist die perfekte Lösung für uns, weil wir wirklich nur das drucken, was wir auch brauchen“, so Lais Kriwat.

"Auspacken" der Gedruckte Einlage
„Im ersten Schritt war unser Ziel, das traditionelle Handwerk zu digitalisieren. Das bedeutet, die Form unserer Einlagen, also die spezifischen Einlagentypen in den Computer zu übertragen und am Ende tatsächlich am 3D-Drucker auszudrucken. In den nächsten Schritten wird es so sein, dass wir ganz neue Produkte schaffen werden, die nur auf der Basis der 3D-Technologie basieren“, stellt Kriwat in Aussicht.
Die Gestaltungsfreiheit des SLS-3D-Drucks ermöglicht unter anderem die Umverteilung des Drucks beim Gehen, individuelle Premium-Produkte, bestimmte Arten von Stützen, die sich mit traditionellen Methoden nicht fertigen lassen, sowie dünnere Produkte, die dennoch optimalen Halt für den Fuß beim Joggen oder Fußball bieten. „Ich freue ich mich extrem darauf, neue Innovationen auf den Markt zu bringen, die vielleicht vor 15 Jahren gar nicht so möglich waren. Dinge, die wir uns heute vielleicht gar nicht vorstellen können, werden schon bald Wirklichkeit.“
Über die Kriwat GmbH
Die Kriwat GmbH ist ein auf orthopädische Schuhtechnik spezialisiertes Sanitätshaus mit Sitz in Kiel. Michael Kriwat gründete das Unternehmen 1987 als einer der ersten Fachleute Deutschlands für die Schrittanalyse auf dem Laufband, sowohl für Hobby- als auch professionelle Sportler. Seit Anbeginn zeichnet sich das Unternehmen durch seinen Fokus auf die Kombination von Leistungssport mit innovativer medizinischer Forschung aus.
Das Unternehmen betreibt sechs Standorte in Kiel, Hamburg und Preetz mit 65 Mitarbeitenden und hat sein Angebot auf die personalisierte Patientenversorgung in den Bereichen Bandagen, Einlegesohlen, Orthesen und orthopädisches Schuhwerk ausgedehnt.
