Diese billig und schnell herzustellenden Plasmasensoren könnten Wissenschaftlern helfen, das Wetter vorherzusagen oder den Klimawandel zu untersuchen.
Forscher haben einen 3D-gedruckten Plasmasensor für Raumfahrzeuge in der Umlaufbahn entwickelt, der genauso gut funktioniert wie die wesentlich teureren Halbleitersensoren. Diese langlebigen, präzisen Sensoren könnten auf kostengünstigen, leichten Satelliten, den so genannten CubeSats, eingesetzt werden, die häufig für die Umweltüberwachung oder Wettervorhersage verwendet werden.
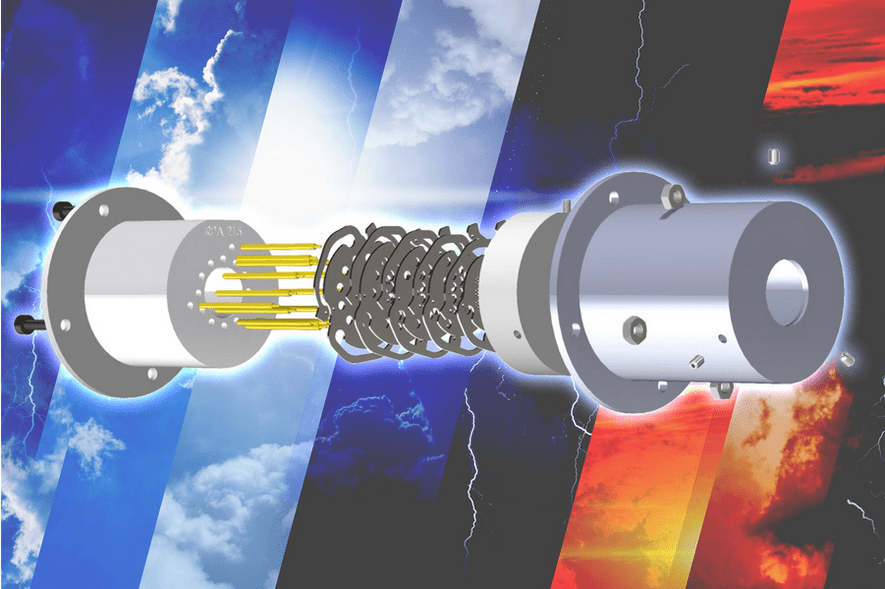
Bildquelle: https://web.mit.edu/
In einer RPA(Retarding Potential Analyzer) durchläuft das Plasma eine Reihe von elektrisch geladenen Maschen, die mit winzigen Löchern versehen sind. Während das Plasma die einzelnen Maschen durchläuft, werden Elektronen und andere Teilchen abgezogen, bis nur noch Ionen übrig bleiben. Diese Abbildung zeigt, wie die Maschen in das RPA-Gehäuse passen, das die Maschen ausrichtet.
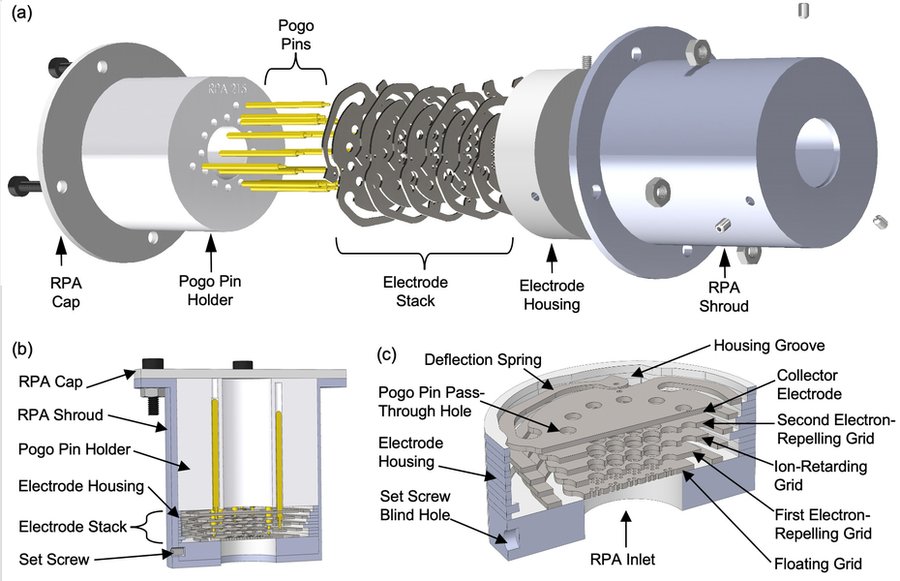
Bildquelle:https://web.mit.edu/
Die 3D-gedruckte und lasergeschnittene Hardware schnitt genauso gut ab wie hochmoderne Halbleiter-Plasmasensoren, die in einem Reinraum hergestellt werden, was sie teuer macht und eine wochenlange, komplizierte Herstellung erfordert. Im Gegensatz dazu können die 3D-gedruckten Sensoren innerhalb weniger Tage für einige Dutzend Dollar hergestellt werden.
Aufgrund ihrer geringen Kosten und der schnellen Herstellung sind die Sensoren ideal für CubeSats. Diese kostengünstigen, leichten und stromsparenden Satelliten werden häufig zur Kommunikation und Umweltüberwachung in der oberen Erdatmosphäre eingesetzt.
Die Forscher entwickelten die RPAs unter Verwendung eines glaskeramischen Materials, das haltbarer ist als herkömmliche Sensormaterialien wie Silizium und Dünnfilmbeschichtungen. Durch die Verwendung der Glaskeramik in einem Herstellungsprozess, der für den 3D-Druck mit Kunststoffen entwickelt wurde, konnten sie Sensoren mit komplexen Formen herstellen, die den großen Temperaturschwankungen standhalten, denen ein Raumfahrzeug in der unteren Erdumlaufbahn ausgesetzt ist.
"Die additive Fertigung kann für die Zukunft der Raumfahrt-Hardware einen großen Unterschied machen. Manche Leute denken, wenn man etwas in 3D druckt, muss man Abstriche bei der Leistung machen. Aber wir haben gezeigt, dass das nicht immer der Fall ist. Manchmal gibt es keine Kompromisse", sagt Luis Fernando Velásquez-García, leitender Wissenschaftler in den Microsystems Technology Laboratories (MTL) des MIT und Forschungsleiter der Forschungsarbeit, in dem die Plasmasensoren vorgestellt wurden.
Vielseitige Sensoren
Ein RPA wurde erstmals 1959 bei einer Weltraummission eingesetzt. Die Sensoren erkennen die Energie von Ionen oder geladenen Teilchen, die in einem Plasma schweben, einer überhitzten Mischung von Molekülen in der oberen Erdatmosphäre. An Bord eines Raumfahrzeugs wie dem CubeSat messen die vielseitigen Instrumente die Energie und führen chemische Analysen durch, die Wissenschaftlern bei der Wettervorhersage oder der Überwachung des Klimawandels helfen können.
Die Sensoren bestehen aus einer Reihe von elektrisch geladenen Maschen, die mit winzigen Löchern versehen sind. Wenn das Plasma durch die Löcher strömt, werden Elektronen und andere Teilchen abgezogen, bis nur noch Ionen übrig bleiben. Diese Ionen erzeugen einen elektrischen Strom, den der Sensor misst und auswertet.
Entscheidend für den Erfolg eines RPA ist die Gehäusestruktur, die die Maschen ausrichtet. Sie muss elektrisch isolierend sein und gleichzeitig plötzlichen, drastischen Temperaturschwankungen standhalten können. Die Forscher verwendeten ein druckbares, glaskeramisches Material, das diese Eigenschaften aufweist, das so genannte Vitrolite.
Vitrolite wurde Anfang des 20. Jahrhunderts entwickelt und häufig für bunte Kacheln verwendet, die in Art-Déco-Gebäuden häufig zu sehen waren.
Das haltbare Material kann auch Temperaturen von bis zu 800 Grad Celsius standhalten, ohne zu zerfallen, während die in Halbleiter-RPAs verwendeten Polymere bei 400 Grad Celsius zu schmelzen beginnen.
"Wenn man diesen Sensor im Reinraum herstellt, hat man nicht den gleichen Freiheitsgrad bei der Definition von Materialien und Strukturen und deren Zusammenspiel. Möglich wurde dies durch die neuesten Entwicklungen in der additiven Fertigung", sagt Velásquez-García.
Herstellung neu überdenken
Beim 3D-Druckverfahren für Keramik wird normalerweise Keramikpulver mit einem Laser beschossen, um es zu Formen zu verschmelzen. Bei diesem Verfahren bleibt das Material jedoch oft grob und es entstehen Schwachstellen aufgrund der hohen Hitze des Lasers.
Stattdessen verwendeten die MIT-Forscher die Kübelpolymerisation, ein Verfahren, das vor Jahrzehnten für die additive Fertigung mit Polymeren oder Harzen eingeführt wurde. Bei der Kübelpolymerisation wird eine 3D-Struktur schichtweise aufgebaut, indem sie wiederholt in einen Kübel mit flüssigem Material, in diesem Fall Vitrolite, getaucht wird. Nach jeder Schicht wird das Material mit ultraviolettem Licht ausgehärtet, und dann wird die Plattform erneut in den Bottich getaucht. Jede Schicht ist nur 100 Mikrometer dick (etwa der Durchmesser eines menschlichen Haares), was die Herstellung glatter, porenfreier, komplexer Keramikformen ermöglicht.Da die Sensoren billig zu produzieren waren und so schnell hergestellt werden konnten, stellte das Team vier verschiedene Prototypen her.
Ein Design war besonders effektiv bei der Erfassung und Messung eines breiten Spektrums von Plasmen, wie sie z. B. ein Satellit in der Umlaufbahn vorfindet, während ein anderes für die Erfassung extrem dichter und kalter Plasmen geeignet war, die normalerweise nur mit hochpräzisen Halbleitergeräten gemessen werden können.
Diese hohe Präzision könnte 3D-gedruckte Sensoren für Anwendungen in der Fusionsenergieforschung oder im Überschallflug ermöglichen. Velásquez-García fügt hinzu, dass das Rapid-Prototyping-Verfahren sogar zu mehr Innovation bei der Konstruktion von Satelliten und Raumfahrzeugen führen könnte.
"Wenn man innovativ sein will, muss man in der Lage sein, zu scheitern und das Risiko zu tragen. Die additive Fertigung ist eine ganz andere Art der Herstellung von Weltraumgeräten. Ich kann Hardware für die Raumfahrt herstellen, und wenn sie scheitert, macht das nichts, denn ich kann sehr schnell und kostengünstig eine neue Version herstellen und das Design wirklich verbessern. Das ist ein idealer Sandkasten für Forscher", sagt er.
Obwohl Velásquez-García mit diesen Sensoren zufrieden ist, möchte er in Zukunft den Herstellungsprozess verbessern. Durch eine Verringerung der Schichtdicke oder der Pixelgröße bei der Glaskeramik-Behälterpolymerisation könnte komplexe Hardware entstehen, die noch präziser ist. Darüber hinaus würde die vollständig additive Fertigung der Sensoren deren Kompatibilität mit der Herstellung im Weltraum ermöglichen. Er möchte auch den Einsatz künstlicher Intelligenz erforschen, um das Sensordesign für bestimmte Anwendungsfälle zu optimieren, z. B. um ihre Masse stark zu reduzieren und gleichzeitig ihre strukturelle Stabilität zu gewährleisten.
Wollen wir in Kontakt bleiben?
Starte am besten gleich hier.
Du suchst Unterstützung im Bereich 3D-Druck? Oder benötigst du ein digitales 3D-Modell um dein Projekt weiter voranzutreiben?
Es ist egal in welcher Phase du dich gerade befindest - Gern unterstütze ich dich bei der Umsetzung deiner eigenen Ideen und Projekte.